QK Honeycomb Products - North Lincolnshire
Locker doors, worktops… These are items in your caravan or motorhome that you see and use daily. What you might not realise is that these panels are all produced in the UK and all the technology behind to make them lightweight but still strong for every day use. In this visit, Simon and Lee discover all the processes and technology involved in making your leisure vehicle panels up to 50% than traditional solid ones.
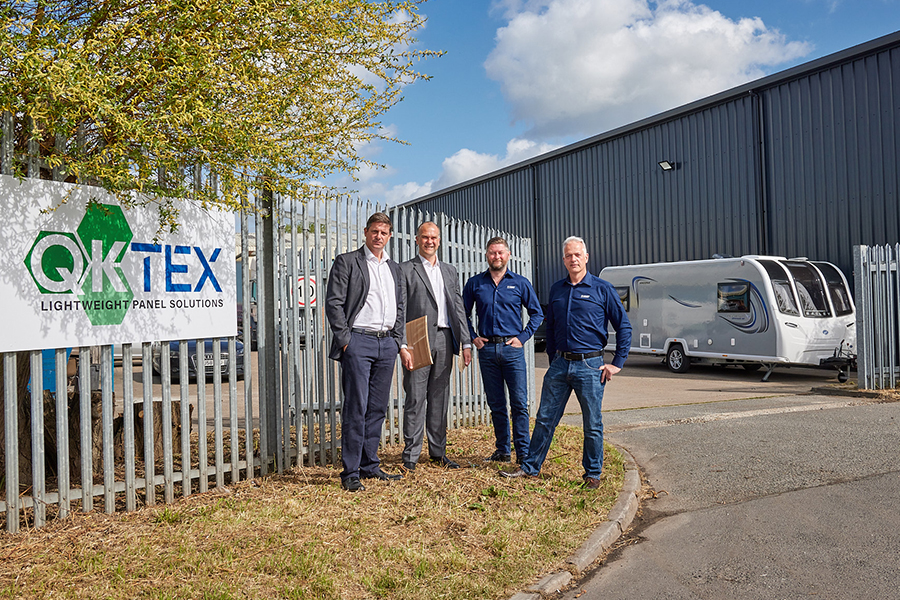
SIMON: Before we start with this interview, there is an elephant in the caravan we need to acknowledge… The good news is that Greg from QK is a very keen caravanner, but sadly, he doesn’t own a Bailey. So Greg, that’s unforgivable.
GREG: My apologies…
SIMON: But, in all seriousness, this is really good news that our suppliers, like Wayne from BCA yesterday who owns a motorhome, or Greg and his caravan, are users of leisure vehicles so it gives you the chance to firstly see the products in situ in the final vehicle but also it gives you a real head start in terms of design because you are looking at it from an owners perspective, so that really is a good thing.
LEE: Lee would you like to explain what you make here at QK as I didn’t realise how complex your panels are!
GREG: Sure. If you look at a cross section of one of your caravans curved locker doors, you can see you have a wood frame on the outside and in the centre you have a lightweight honeycomb core. This is made from reconstituted recycled cardboard, and this enables us to deliver a lightweight product that is 50% lighter than any solid panel product that you could put in a caravan. And that’s obviously a key factor. As all caravanners know, your towing weight is an essential and important factor to consider.
And then the veneer and the finish we put over the top depends on the particular model and the customer’s preference, but we have a multitude of different finishes that we can apply, and these are glued and pressed into the frame and the honeycomb, cut, edged and finished.
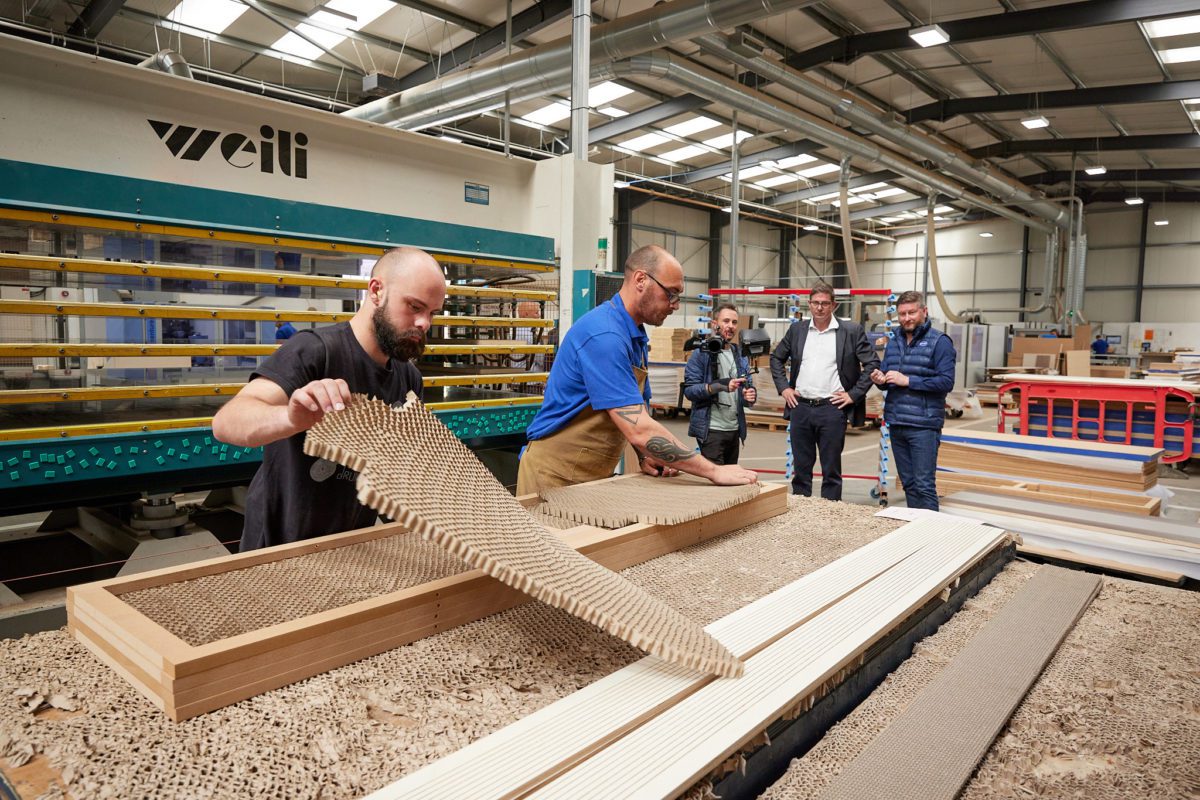
SIMON: Approximately, how long does it take to make a panel?
GREG: Making a single panel from process to process would take a couple of hours but then we have to add 12 hours or more for the fully cured time field.
LEE: With lightness in mind, what tests do you do to make sure they are rigid enough for everyday caravan use?
We use external bodies to help us test the integrity of the structure. We’ve done tests on the glueing, heat tests, weight tests, … and we ensure there is a structural insert wherever the panel or the door is going to be fixed in the caravan or motorhome so essentially, it’s solid to solid meaning the actual attachment point is still a solid point. This ensures there is no compromise by using the centre of a piece, where you have the honeycomb, as part of your structural mechanism. That’s just holding the form and the shape of the door or the panel.
SIMON: Apart from locker doors, what else do you make?
GREG: We also make table tops.
SIMON: And are these made in exactly the same way?
GREG: The principle is essentially the same using different materials. But if you took a table top apart, you would see the same sort of internals as you see in a locker door.
SIMON: And you also make kitchen worktops, washroom worktops… Your panels are everywhere in this van… Exactly how many panels have you made in this Pegasus Grande SE Ancona?
GREG: In the model we’re sitting in right now, we’ve made 33. That’s 11 worktops, 19 doors and 3 back panels.
SIMON: Is that the average?
GREG: The most recent supply was 55 into a model. It could also be a bit more than that. But the average for us would probably be 30 to 40 units into each model.
"On average there are between 30 and 40 QK lightweight panels in every Bailey caravan"
SIMON: And obviously not the same panel either… There is a lot of variation…
GREG: Yes, differences in shape, finishes, …
SIMON: Talking a bit more about variation, until recently you have just been making flat panels and flat worktops but recently you invested a lot in some new very swish equipment which allows you to make shaped panels…
GREG: Yes. As part of investing generally in the facility, we have also invested in the capability of making curved panels: New presses, new post-forming machines, new glueing technology… And that’s enabled us to move from just supplying the flat content within a caravan to the curved panels as well and bringing forward the same honeycomb lightweight properties into those curved products.
SIMON: From our point of view that’s fantastic news because you are a UK supplier so that’s investing in UK industry . And that has allowed us to take back some of our production from Europe and give it to you, so we are getting UK product which is great for the economy but also helps the environmental footprint for all businesses.
GREG: Yes, absolutely. We have invested to be able to support UK manufacturers like yourself. We are very proud that we have done that.
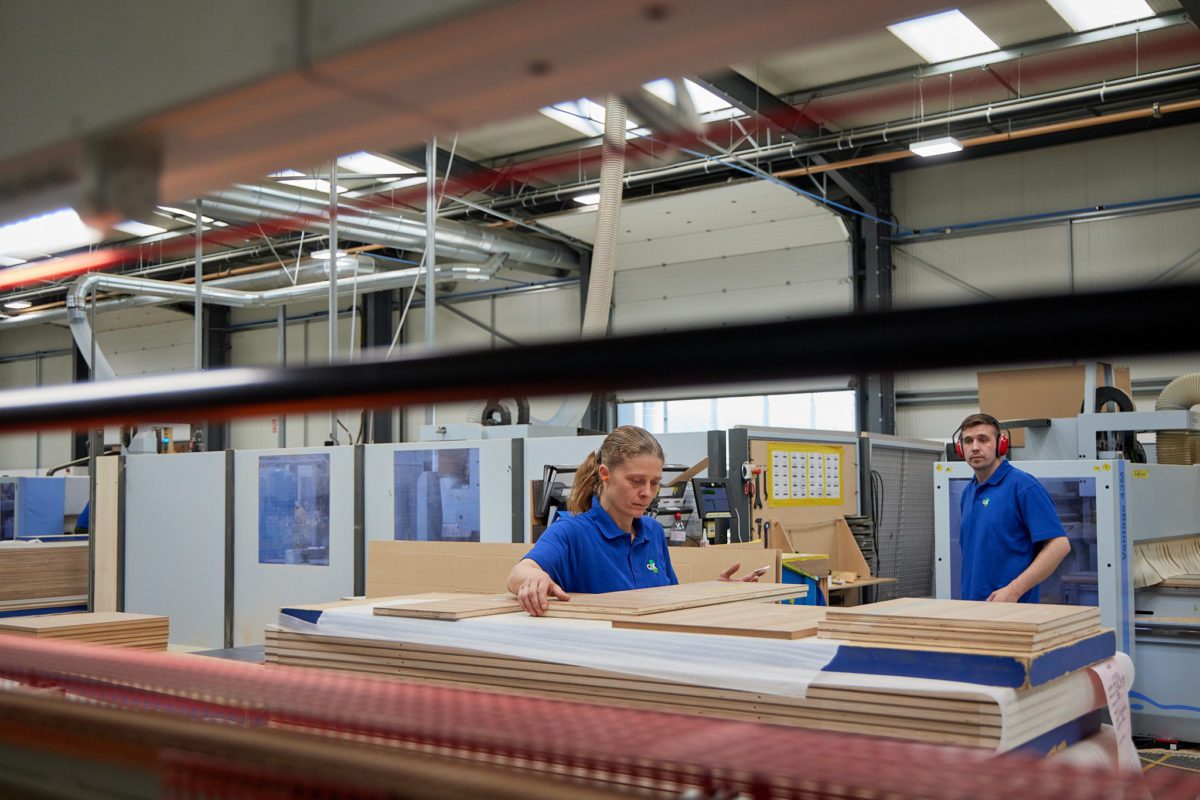
SIMON: One of the advantages of having a UK supplier is that it negates some of the uses related to Brexit. So how has that affected you as a business?
GREG: It’s been more administration and logistical cost… Changes in exchange rate fluctuations, the additional cost of materials… So it’s been more expensive and slow to bring materials in from Europe where we still have a supply chain, but we are trying to localise our supply chain as much as possible in the UK. It’s an advantage for us to deal with UK businesses ahead of European businesses.
"With Brexit, it’s been more expensive and slow to bring materials in from Europe where we still have a supply chain, but we are trying to localise our supply as much as possible"
SIMON: I supposed that’s manageable and that has been planned but what about COVID? Because that obviously wasn’t planned…
GREG: We were concerned about the health repercussions and the disruption of business. So we tried to keep people safe following all the government guidelines at the same time as trying to maintain production and supply to our customers.
Many of our customers, like Bailey, experienced similar issues to us. So we worked with them, we worked through it and we’re now please to say we’re moving forward and looking forward to a better future as we come out of the COVID impacts we have all suffered.
SIMON: Regarding the investment you have made recently, I don’t imagine that machinery is cheap…
GREG: Investing in that timeframe of Brexit and the pandemic… We’ve invested £2m in the facilities here so it’s been significant at the time all that has been going on. That’s because we are committed to the industry and to our business and to our customers.
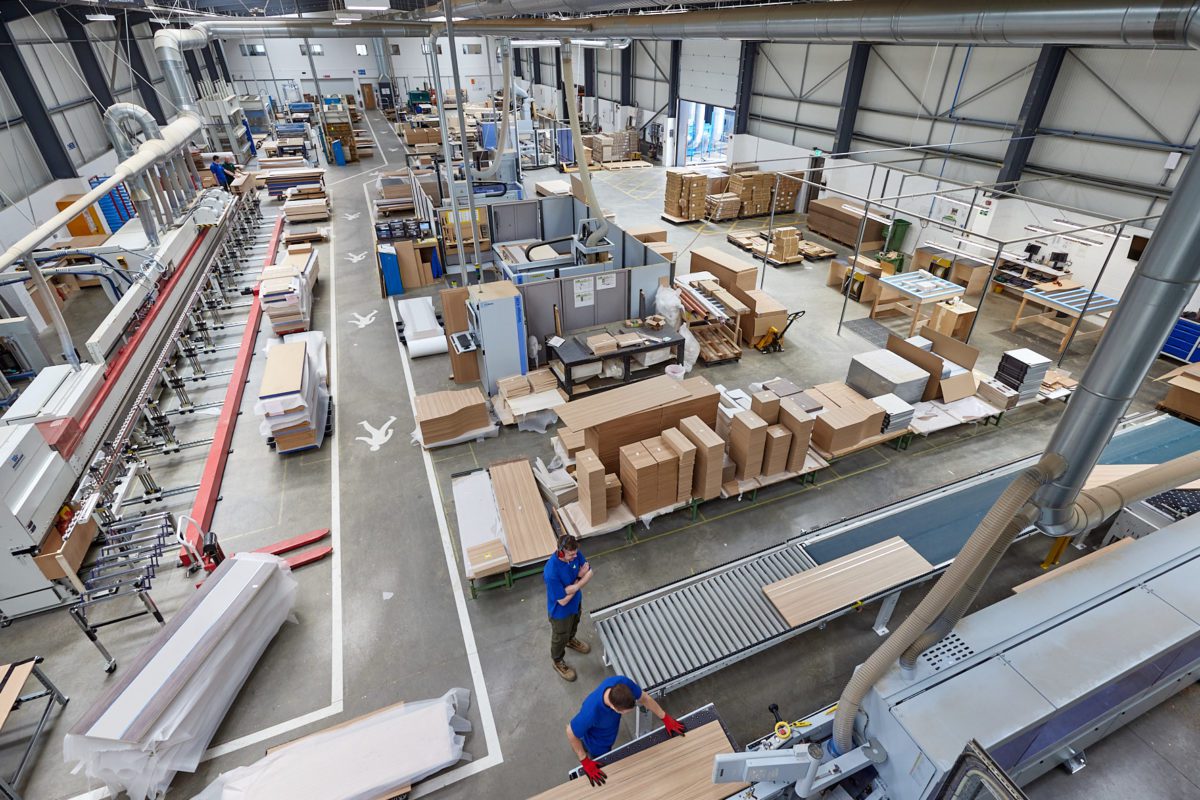
SIMON: I appreciate you are part of the Tex Group and you have three divisions: One is engineering, one is plastics and QK is part of the boards and panels division. So in addition to caravans and motorhomes, where else do you sell you lightweight panels?
GREG: The other sectors that we supply is furniture. For example, office furniture. We also supply into the point-of-sale sector and exhibitions and displays.
LEE: How many years have you been making caravan specific panels for?
GREG: The group bought QK business in 1989 and we have been making caravan panels ever since.
LEE: So your experience goes back to when Bros were in the charts… That’s quite some time.
END
Images from our day at QK
Take a look at the gallery below to see images from our day at QK Honeycomb Products. Hover over the information icon on each photo to read the caption.
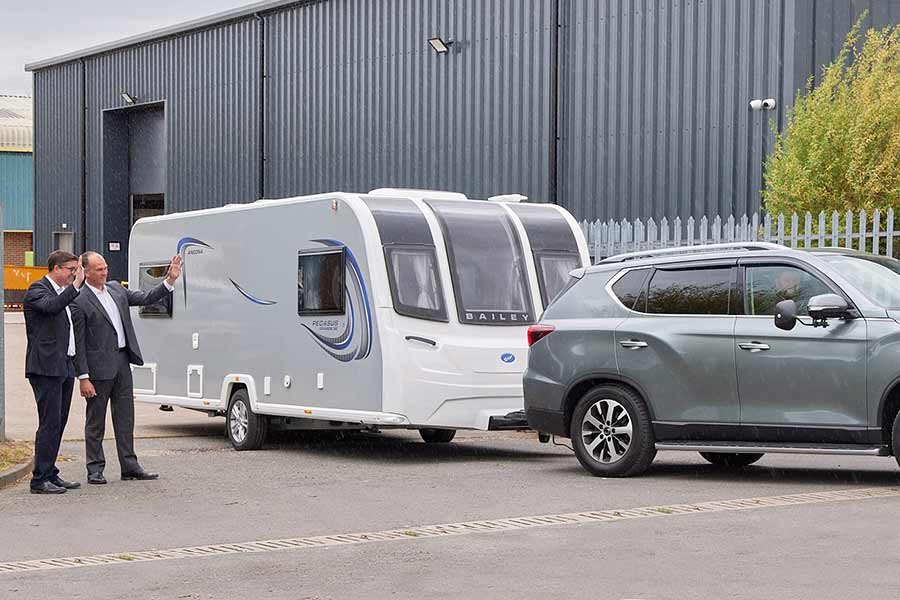