Sustainable Manufacturing
By way of example, research by The National Caravan Council suggests that emissions for a 1,000+ mile journey from London to the North of Scotland with a family of four in a small saloon car towing an appropriate caravan produces only 38% (0.36 tonnes) of the C0² output of a similar distanced flight, which would produce emissions of nearly a ton (0.96 tonnes).
In order to sustain our industry going forward, it is important that we work in harmony with nature to ensure that it can continue to be enjoyed by future generations
At Bailey, we remain committed to playing our part in this process by reducing the environmental footprint of our operations and striving to make our leisure vehicle products as sustainable as possible.
Over recent years we have undertaken a range of initiatives designed to reduce our impact on the environment, covering our products, our sites and our culture.
Green Products
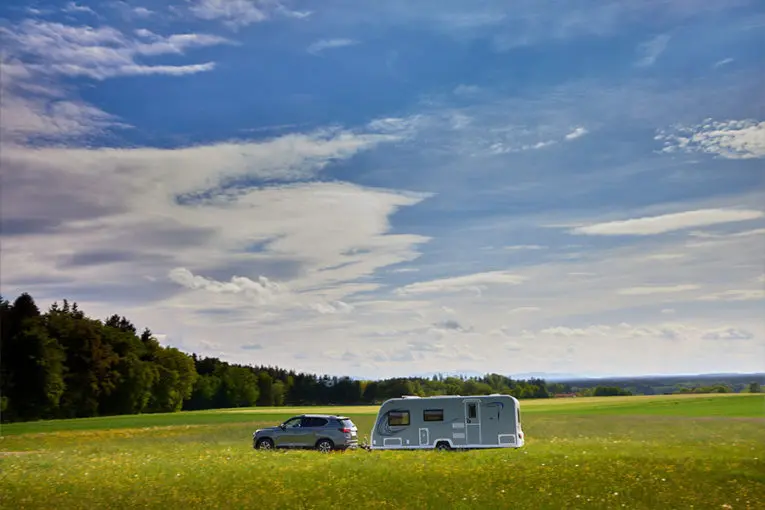
We manufacture leisure vehicles which are up to 75% recyclable at end-of-life
As much as possible we use renewable materials, including FSC certified timber sourced from sustainable forests, water based solvent-free adhesives in our body shell panel construction process, recycled composite plastic bodyshell panel framework extrusions and recyclable paper coated plywood furniture board in our manufacturing process.
Green Site
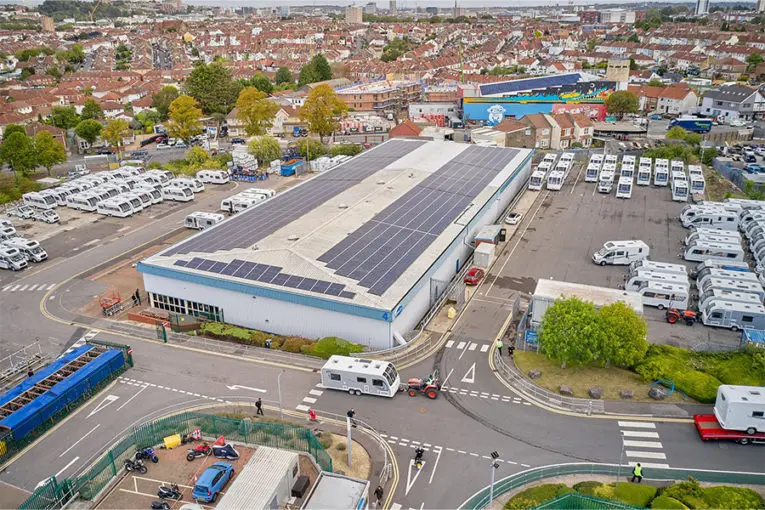
Lowering the impact of our operations
Solar power, LED Lighting and 100% renewable energy supply are some of the ways we are reducing the environmental footprint of our business across our three sites in Bristol.
Green Culture
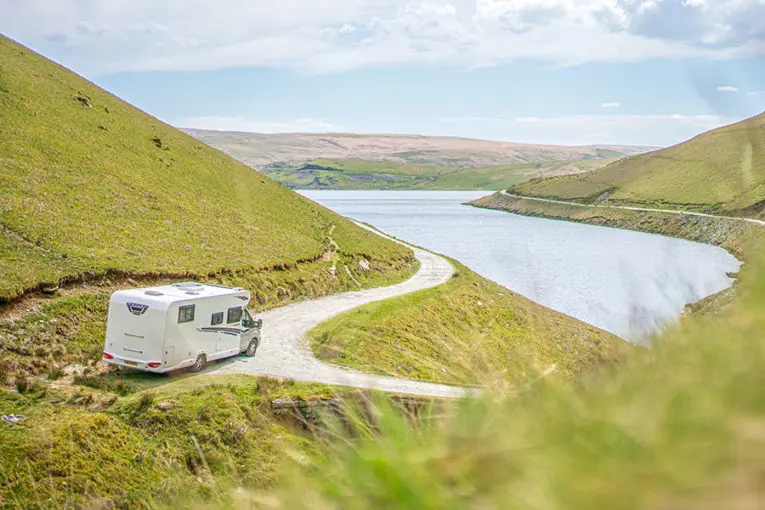
What is good for the planet is also good for business
Which is why waste reduction and energy management remain central to our thinking. Bailey was the first company in our industry to implement a waste recycling scheme and in doing so we have been able to halve the amount sent to landfill sites. Annually this equates to 720 tons of waste products which is the equivalent in weight to 480 caravans or 205 motorhomes.
Supporting the Woodland Trust
As part our efforts to reduce the environmental impact of our operations, since 2022, Bailey has been supporting the work of the Woodland Trust to protect and restore native woodlands across the UK. This year’s donation of £5,575 helps to safeguard approximately 7,830 trees, with the potential to absorb an estimated 223 tonnes of CO2e emissions.
Find out more about the work of the Woodland Trust here
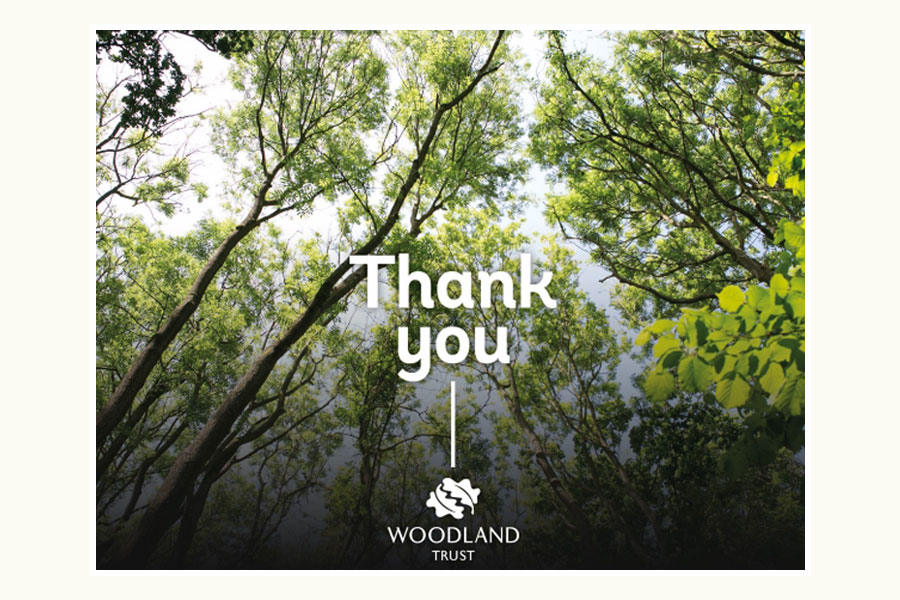