Bailey of Bristol Invests £2.5 Million in CNC Upgrade to Transform Furniture Panel Production
This significant upgrade marks a transformative step forward in efficiency, quality, and safety for the UK’s longest established leisure vehicle manufacturer.
The new CNC routers, supplied by German engineering specialist HOMAG, replace seven ageing machines that had been in operation for over 20 years. These legacy units required manual loading, were increasingly prone to breakdowns, and limited Bailey’s ability to scale production. The state-of-the-art replacements are fully automated, delivering faster, more precise and more reliable panel cutting while dramatically improving operator safety.
“This investment is a major milestone in the modernisation of our factory,” said Nick Howard, Managing Director at Bailey of Bristol. “The new system allows us to increase production volumes, improve quality, reduce waste, and create a safer and more efficient working environment for our team.”
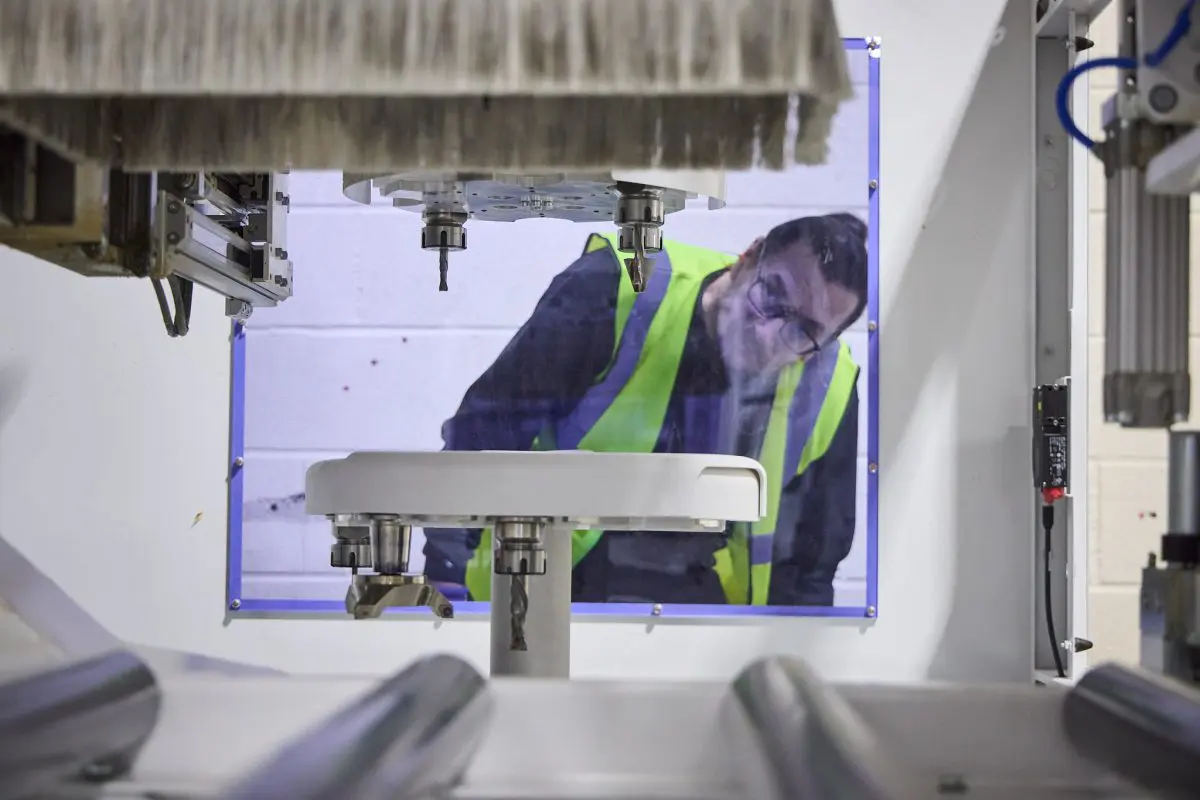
Smart Automation and Safer Operations
The CNC machines are arranged in a high-efficiency line, integrated with an automated, 44-station palletised plywood handler. This intelligent storage and retrieval system runs 24 hours a day, automatically shuffling material to feed each machine exactly what it needs. Twin bridges allow stock to be replenished and consumed simultaneously within a single shift, removing the need for extra hours dedicated to stock handling.
Panels are now loaded automatically, eliminating manual lifting and keeping operators at a safe distance from potential hazards. All machines are programmed and controlled remotely from the office, removing the need for on-the-ground loading and significantly boosting operational efficiency.
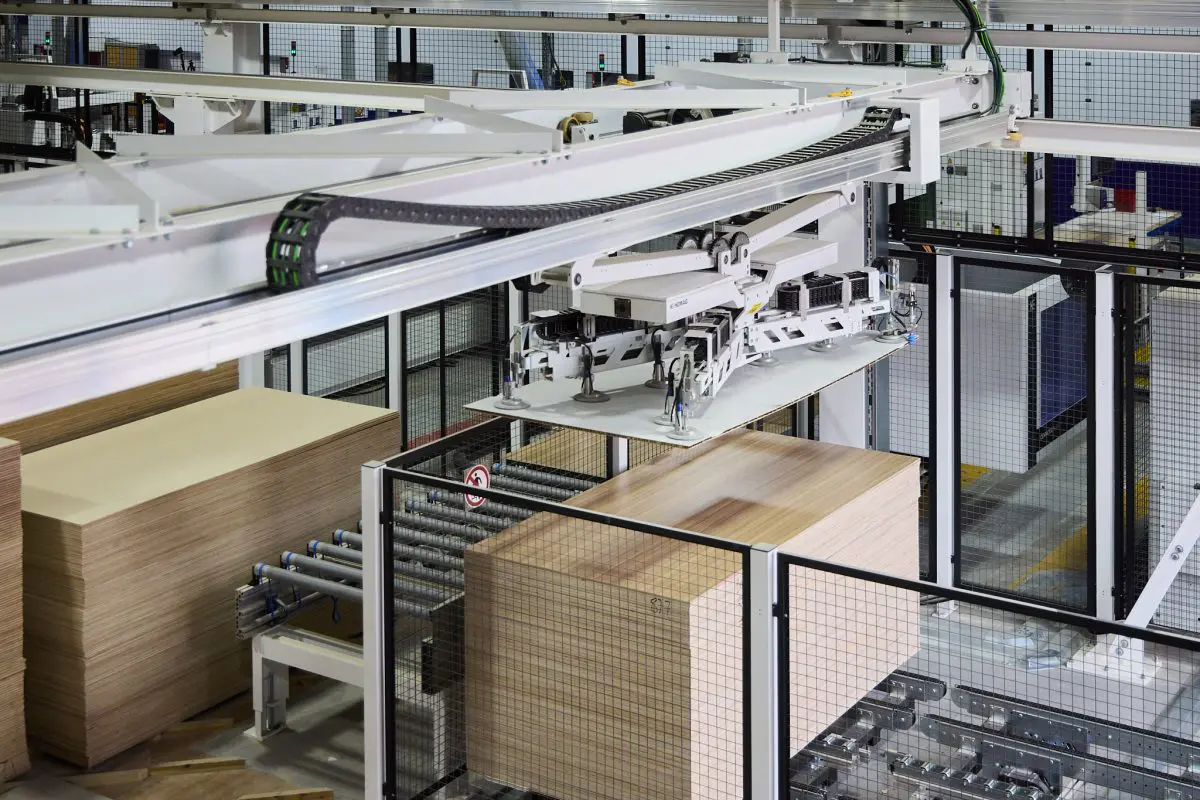
Measurable Improvements
- Quality & Waste Reduction: With increased accuracy and consistency in cutting, damage and waste have both been substantially reduced.
- Efficiency Gains: The five machines now produce around 5,800 panels a day (an average of one every 10 seconds) while consuming less power, thanks to HOMAG’s energy-optimising features.
- Workplace Safety: With automated lifting and extraction systems in place, the working environment is safer, cleaner and more ergonomic.
- Sustainable Manufacturing: The system maximises how many panels can be cut from each plywood sheet, and all sawdust is extracted to keep the space clean and reduce airborne particulates.
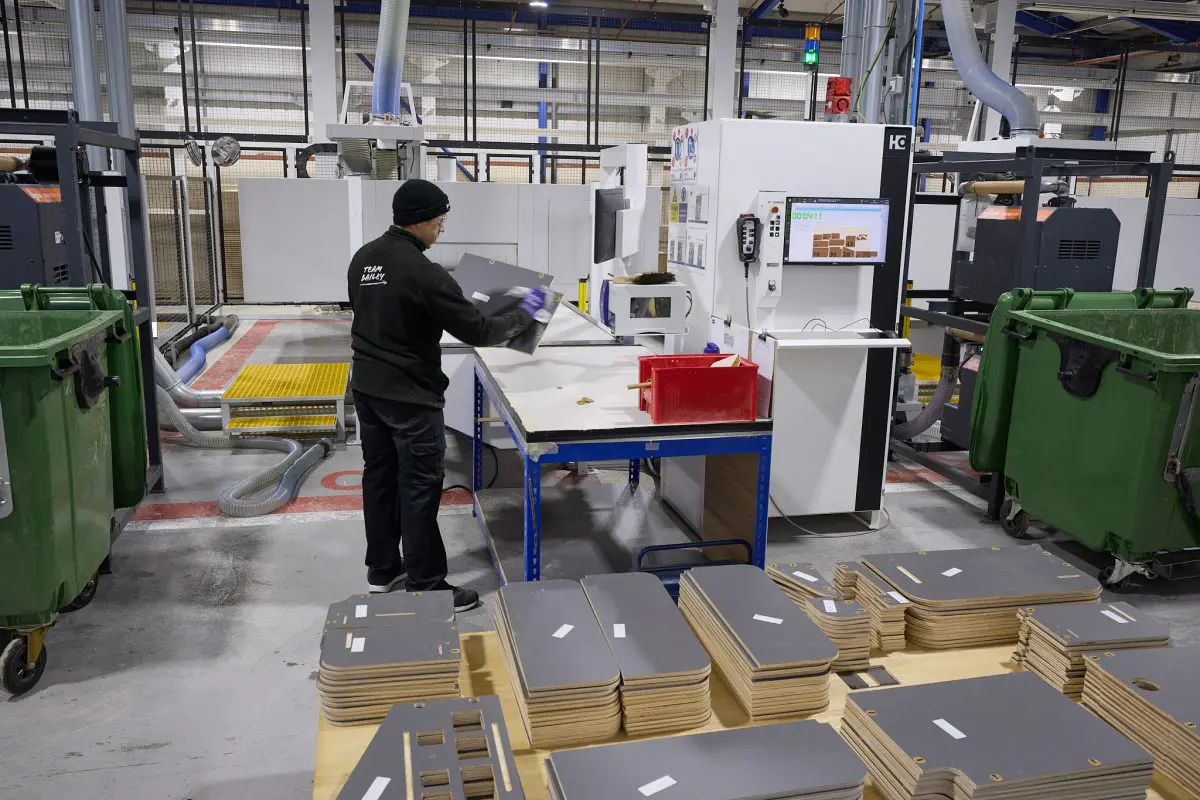
Supporting Future Growth
The investment doesn’t just improve current processes, it lays the groundwork for future expansion. The increased speed and automation create capacity for a wider product portfolio and higher volumes, ensuring Bailey remains agile in a competitive market.
At the same time, an additional CNC machine has been installed at Bailey’s Clevedon site specifically to handle smaller components such as ceilings and bulkheads for the Endeavour campervan range. This allows larger CNC routers to focus on high-volume jobs, improving efficiency across both facilities.
This investment underlines Bailey of Bristol’s ongoing commitment to quality craftsmanship, employee wellbeing, and environmentally conscious manufacturing, all while maintaining production here in the UK.
Previous
News & Events
Latest news & events
See all news & events10 Year Birthday Weekend at Winchester Caravans
COLDEN COMMON, MAIN ROAD, WINCHESTER
2026 Caravan & Motorhome Big Reveal Show at Grantham’s
SPITTLEGATE LEVEL
GRANTHAM
The BIG Event 2025 at Stowford Leisure
ELY VALLEY ROAD, LLANTRISANT, RHONDDA CYNON TAF
Free Stay in Pembrokeshire with Tenby Tourers
Crofty Showground, Llanteg, Narberth, Pembrokeshire