Building a Bailey, Part One
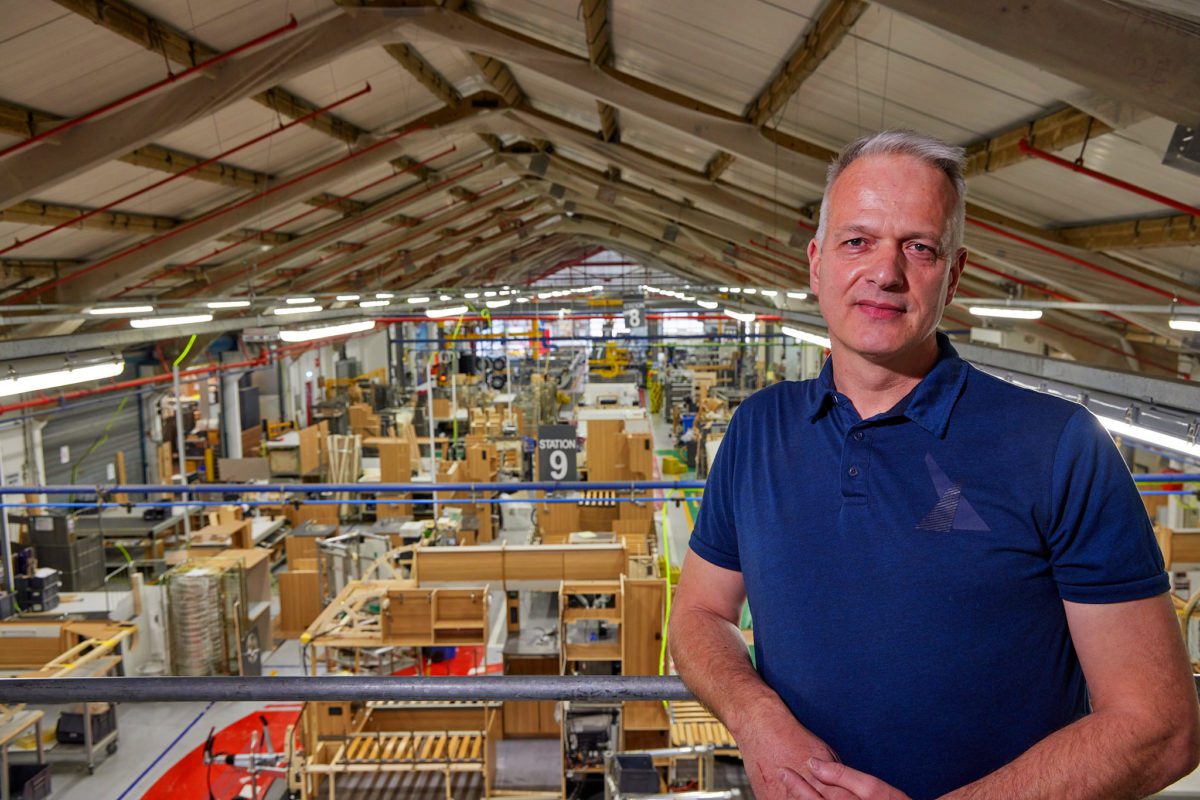
In a bizarre series of events, renovating our 1967 Bailey Maestro was the catalyst behind my day on the Bailey of Bristol production line. Much to my wife’s disgust, our patio was renovation HQ for our 60s’ van, although I’d be swapping wonky paving for twenty-five workstations, twelve of which I would be experiencing in a single day. Instead of my son, Charlie, being my workmate, I would be joining 158 seasoned professionals. It promised to be a very different day indeed.
To work on the production line, the HR and Health & Safety departments asked that I follow the route taken by all employees before being given the green light. Far from the classroom presentation being a list of do’s and don’ts, the structure was employee-focused and covered hot topics such as wage progression and procedures that ensure each employee is looked after, both mentally and physically. A goodie bag was a nice touch, and along with a new uniform, it concluded induction day. When asked if I had any questions, I wondered if any employee had tackled twelve stations on his or her first day. ‘No’ was the answer. I would be the first to attempt such an undertaking.

With my alarm set for 05:45, a time I’m blissfully unaware of under normal circumstances, I was thankful for the unusual pitch the Bailey Phoenix occupied – a spot within the Bailey car park. I was also incredibly grateful for the coffee that arrived at 06:30, courtesy of team leader Craig, who would be instructing me later that day.
Bleary-eyed and mimicking my first day at school, my new shoes shuffled to the Toolbox Talk session at 07:00 sharp. Various production topics were covered, many of which went over my head, but one nugget of information stuck with me – today’s target was twenty-five caravans. I feared ham-fistedness on my part would affect this figure, as many a future holiday relied on an accurate daily figure.

If Homes Under the Hammer and The Great British Bake Off have taught me anything, a structure of any kind needs a firm base. Caravan construction is no different, and the AL-KO chassis provides this essential support. The chassis rails, axles, and road wheels are packaged separately and assembled at the Bailey factory on a jig. Introducing me – a newbie – to a well-oiled production team slowed progress a little as the hitch and axle were added to the frame rails, with each bolt torqued to the correct setting and marked accordingly.
As I was helping to prepare the chassis, Station 4C was preparing the floor, a location I would move to during the following cycle change. Having spent the day as a workshop apprentice at Stowford Farm Meadows, helping the technician service our Bailey Phoenix for a Caravan & Motorhome Club feature, I thought I was familiar with many caravan components. Still, I discovered many new processes at the factory resulting from years of research and development. It may sound like a small thing, but I didn’t realise sealant was applied between AL-KO chassis rails and the floor to keep squeaking to a minimum. Corner steadies are added, and various fixings ensure the floor and chassis are integral at each station further along the line.

The floor is turned 180 degrees, ready for various services to be added at the next station. My brain was already beyond capacity and trying to follow instructions as the Truma Combi, and associated pipework was fitted only added to my frazzled grey matter. I could feel beads of sweat forming under my Bailey-branded hardhat, and the blur of pipework routes and bed base fixings is still unclear to this day. Granted, I was being thrown in at the deep end, but every worker’s skill was immediately apparent as they double-checked each component I had fitted and did so with a level of calm that felt alien at the time.
With the first line completed, a relative calm descended. Not just for me but for Section Chief Jason, who was tasked with steering me through the chosen stations. A firm foundation is everything, and the importance of making everything line up perfectly so that walls, roof, and additional kit fit as intended is felt at each station. These guys and girls work with a level of care and enthusiasm that I hadn’t necessarily expected if I’m honest. Even when Jason introduced me to each station and told the team to get me as hands-on as possible, the team members were visually checking angles and discreetly fitting bolts, when sitting back for the duration of the cycle would’ve been all too easy.
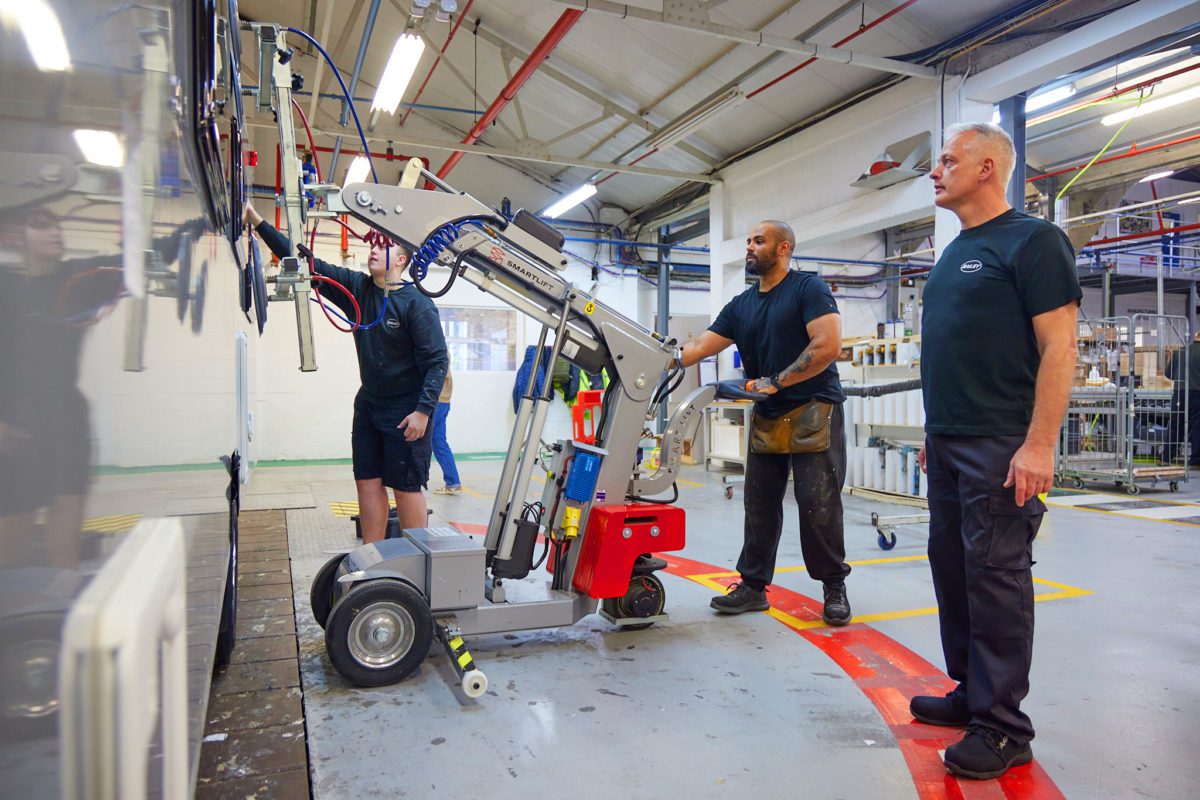
With Jason undoubtedly pleased to pass me on to another section, I had little idea of what was in store. In Part Two of Building a Bailey, I’ll be pitting my remedial Ikea assembly skills against a cabinet maker with 18-years of experience, experiencing a yoga-like workout as I fit the all-important Alu-Tech bodyshell, and discovering that having an early morning coffee hand-delivered to my caravan always comes at a price.
Previous
8ft Wide Caravans: Is a Bigger Caravan Better in 2022?
Next
Building a Bailey, Part Two
Latest news & events
See all news & eventsChichester Caravans Uckfield Spring Sale
LONDON ROAD, UCKFIELD, EAST SUSSEX